
OUR STORY
Polygon Development Group is a fully-integrated real estate construction and development company.
We are a focused team of professionals who excel at creating and orchestrating the development process. Our in-house experts span every discipline, from site identification, zoning and entitlements, to master planning, design and construction. A comprehensive understanding of the design/build process allows Polygon Development Group to identify and seize opportunities and capitalize on emerging market trends.
Polygon’s signature mode of operation is hands-on, providing detailed project management that ensures each project is completed to perfection. Tight quality control measures include careful planning and meticulous attention to the most minute details, which results in each project exceeding expectations. With the leadership’s deep understanding of construction laws and regulations, there are no surprises during the development process.
Along with our team of industry experts, Polygon also maintains trusted relationships with the full gamut of construction subcontractors and real estate professionals in the community. With an established network of architects, engineers, surveyors, construction managers and subcontractors, Polygon has access to every construction and real estate related service professional. Collaborating with regional subcontractors and resources allows Polygon to push projects forward smoothly without hitches.
From start to finish, Polygon effectively coordinates the implementation and completion of every phase of the development and construction process. Our vision is to successfully execute projects with above market returns.
Polygon builds strong relationships with each project. We understand that by transforming properties, we have the power to transform a neighborhood and a community. We seek to add value to every property and share the benefits with every community we join.

A CASE STUDY IN EMERGENCY PROBLEM SOLVING
CREATIVE THINKING AND AGILE MANEUVERS BRING EXPEDITIOUS SOLUTIONS.
​
The Problem:
The onset of the COVID pandemic in March 2020 brought a massive influx of patients to New York City’s healthcare system. In an effort to relieve hospitals, the New York City Office of Emergency Management worked with the U.S. Military and FEMA to establish a temporary field hospital in the Jacob J. Javits Center. The hospital was designed to treat non- COVID, low acuity patients in a non-hospital setting.
However, within days of opening, they were overwhelmed with patients suffering from COVID. Many of these patients required high-volume oxygen supply, far beyond the oxygen bottles and oxygen concentrators which had been installed originally. The medical professionals at the Javits Center needed a way to access and install a sufficient oxygen supply to support high flow oxygen delivery and ventilators.
The Polygon Approach:
From the start of the pandemic, ONE70 Group, a division of Polygon Development Group, was in discussion with the OEM regarding medical gas for other facilities. Well known for their ability to leverage resources, ONE70 was tapped to identify real buildings that could be quickly converted into acute care hospitals. A 280k sf Skilled Nursing Facility development ONE70 was building in the Crown Heights area of Brooklyn was quickly approved for use in treating COVID patients and adapted to meet the urgent need. In addition, ONE70 gutted and rebuilt 25k sf in Boro Park Center for Rehab in only 2 weeks to treat overflow patients from Brooklyn’s Maimonides Hospital.
Calling upon ONE70’s expertise, the medical team reached out in search of a solution for supplying oxygen to the Javits Center.
The Solution:
It took a creative mind to work with the National Fire Protection Association, the State Building and Fire Code and the FDNY regulations to find a place to install oxygen tanks. After surveying the property, ONE70 determined that the concrete slab of the loading dock would be a practical and safe location for the tanks.
At that time, every health system in America was buying up oxygen tanks and components. Most parts had a lead time of six months or more. Thanks to their industry connections, ONE70 was able to procure tanks that could be converted for oxygen use within a week. They also negotiated with an oxygen supplier to fill the tanks as needed. As a temporary measure, the oxygen supplier provided trailers until the tanks could be installed.
Within the temporary hospital, there were no wall boxes or cords available for the internal oxygen delivery system. The experts at ONE70 discovered a medically rated version of flexible medical pipe, which did not require welding. In a creative use of resources, ONE70’s technicians used ambulance oxygen ports with an adapted wall box to wall mount oxygen systems within the cubicles in the Javits center.
The typical lead time to install a bulk oxygen system is six to nine months. ONE70 had oxygen flowing to the Javits Center patients within the first five days. The technicians used temporary measures to turn on oxygen by increments, for the first 30 ICU patients, then 60 patients. By the end of three weeks, the field hospital was completely piped and ready for the big oxygen tanks. Within six weeks of the start of the project, the oxygen tanks were installed and fully operational.
The Javits Center field hospital treated over 1,000 patients over the course of the pandemic.
ONE70’s creative problem-solving and agile workmanship brought relief to many suffering COVID patients.




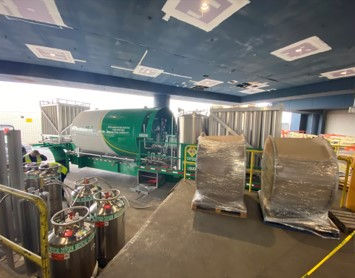


